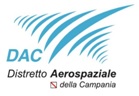
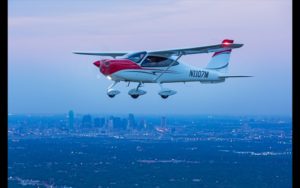
Napoli, 23 giugno 2020 – I materiali compositi, dati i loro alti costi e complessità sono sempre stati appannaggio dei grandissimi produttori aerospaziali di velivoli commerciali, Airbus, Boeing. L’obiettivo del progetto TABASCO (Tecnologie e Processi di Produzione A BASso Costo per Strutture in COmposito per Velivoli Avanzati) è stato quello di ripensare tecnologie e processi di produzione per renderli disponibili anche ai produttori aeronautici dell’Aviazione Generale.
Partito con il velivolo certificato Tecnam P2010, il progetto ha potuto creare nuovi e certificati standard di produzione, portando il P2010 alla certificazione EASA e, in seguito, a quella statunitense FAA. Grazie a questa esperienza, non solo sperimentale, ma anche produttiva con l’utilizzo dei processi e delle tecnologie consolidate attraverso il programma di ricerca e infine con l’attività commerciale sono stati venduti in tutto il mondo 130 aerei P2010.
Con la stessa tecnologia possiamo considerare il numero di oltre 500 velivoli se includiamo anche i modelli, P2008JC, P2008: tutti realizzati in materiale composito. Questi velivoli sono richiesti da scuole di pilotaggio, enti pubblici e utenti privati. I materiali compositi consentono forme più spaziose della cabina e linee accattivanti.
Una nuova conquista della tecnologia e della ricerca applicata made in Campania realizzata attraverso i progetti di sviluppo attivati dal Distretto Aerospaziale della Campania, DAC, in collaborazione con TECNAM, tra i primi 3 produttori al mondo nella categoria Aviazione Generale, uno dei pochissimi produttori certificati ad usare sia il metallo che il composito.
Il progetto del valore di 6 M€ è stato cofinanziato dalla Regione Campania. La compagine di ricerca che lo ha sviluppato è tutta costituita da soci del DAC presieduto da Luigi Carrino. La competenza scientifica è stata contribuita dalle Università di Napoli Federico II, della Campania L. Vanvitelli, del Sannio e dall’Università Parthenope oltre che dal Consiglio Nazionale delle Ricerche (CNR) e dal Centro Italiano di Ricerca Aerospaziale (CIRA). Ha preso parte al progetto anche l’Istituto Nazionale di Astrofisica (INAF) attraverso l’osservatorio Astronomico di Capodimonte pure interessato a introdurre l’uso dei materiali compositi nelle applicazioni di astrofisica. Magnaghi, LAER, Protom, Leadtech, hanno portato il contributo industriale partecipando attraverso i consorzi soci diretti del DAC di cui fanno parte (rispettivamente SAM, Chain, ALI).
TECNAM è tra i primi 3 produttori al mondo nella categoria Aviazione Generale, uno dei pochissimi produttori di velivoli di questa categoria in grado di ottenere certificazione all’uso di compositi da parte dell’Autorità di Navigazione EASA/ENAC.
È ora in uscita il modello di velivolo TECNAM più piccolo che pure fa ampio uso di compositi: il P92 MkII. Si tratta di una ri-edizione del classico P92, velivolo entry-level della flotta TECNAM esempio tangibile dell’applicazione a “basso costo” dei compositi nella produzione di velivoli per Aviazione Generale.
“Il progetto nasce con l’intenzione di proporre nuovi velivoli innovativi e con maggiore appeal per i clienti passare dalle costruzioni in metallo a quelle in materiale composito – spiega Michelangelo Giuliani di TECNAM – Abbiamo realizzato elementi strutturali primari, in particolare fusoliere monoscocca, che vengono realizzate in materiale composito pre-impregnato fibra di carbonio e resina epossidica dando forme aerodinamiche che sono più vicine ai desiderata del progettista e anche più belle dal punto di vista estetico. Il confronto è con i grossi airliner che sono fatti con queste tecnologie. Il punto di partenza è stato il materiale: abbiamo razionalizzato i criteri di selezione del materiale portando alla definizione delle caratteristiche necessarie per soddisfare i requisiti generali di costruzione e, ovviamente, per conto dei costi, della reperibilità e della riparabilità dei materiali. Abbiamo così sviluppato un database proprietario di materiali e processi che possono essere impiegati allo scopo”.
Proprio con l’impiego di questi materiali è nata la prima macchina, P2010, un velivolo 4 posti, monomotore certificato. Il velivolo ha fatto da apripista rappresentando il top della complessità dal punto di vista operativo e tecnologico e, a valle di questo, sono stati realizzati ulteriori due velivoli: il P2008 (versione due posti certificata l’anno successivo al P2010, in tempi ristrettissimi avendo già sviluppato il know-how e oggi viene lanciato il P92MkII, velivolo ultra leggero che adotta le stesse tecnologie costruttive.
“La tecnologia sviluppata e il know-how acquisto permette oggi alla Tecnam – spiega Giuliani – di approcciare nuove ed ulteriori sfide. In Italia, dopo il periodo di incubazione dell’ATR che è stato il primo programma civile con un impatto massivo della carboresina fatto da aziende italiane, ci sono stati altri esperimenti che si sono spinti con la categoria ultraleggera. Il P2010 ha ottenuto la certificazione con dei requisiti stringenti molto prossimi a quelli degli airliner, pur contenendo obiettivi e costi nell’ambito di quella che è l’aviazione generale”
Il progetto, come da statuto, ha realizzato pienamente il trasferimento e l’abilitazione delle tecnologie necessarie. Il database realizzato viene oggi incrementato ed esteso via via che si fanno ricerche e attività sulla base dell’approccio metodologico segnato e, dunque, il percorso di sviluppo consentirà ulteriori estensioni.
Durante lo svolgimento del progetto le macchine sono state certificate con una velocità che ha sorpreso la stessa autorità europea per la proattività delle soluzioni individuate ed adottate. Quelli che erano solamente dati proiettati sulla base di studi hanno trovato conferma nella vita operativa perché uno dei problemi principali delle strutture in materiale composito è il degradamento dovuto alle condizioni ambientali oppure, in caso di incidenti, si teme che il carbonio sia più fragile e impattante per la sicurezza degli occupanti il velivolo.
In realtà i dati statici ci hanno insegnato che la cellula ha risposto bene a tutte le sollecitazioni, con una proposizione non solo per i diportisti, ma anche per le scuole di volo, che rappresentano oggi il principale cliente per la vendita di velivoli realizzati con queste tecnologie. Addirittura un P2010 ha volato da Capua in Pakistan attraversando il deserto con alte temperature ed umidità, dando così ulteriore convalida del prodotto.
“TABASCO si colloca all’interno delle iniziative che il Distretto pone in essere per venire incontro alle esigenze dei soci industriali, in particolare delle piccole e medie aziende – ha detto Claudio Voto del DAC – La crescita in termini di competenza tecnologica delle PMI del settore, supportata dalla conoscenza dei soci scientifico-accademici è associata alla necessità di sostenere i costi che questo processo di crescita collettiva richiede. Proprio queste esigenze hanno spinto alla nascita del Distretto che ha partner scientifici e industriali. Il Distretto vuole realizzare delle sinergie che permettano una crescita complessiva dell’intero settore per essere maggiormente competitivi sul mercato globale. Di qui la necessità di dare supporto alle iniziative di ricerca e trasferimento tecnologico dei soci del Distretto Aerospaziale”.